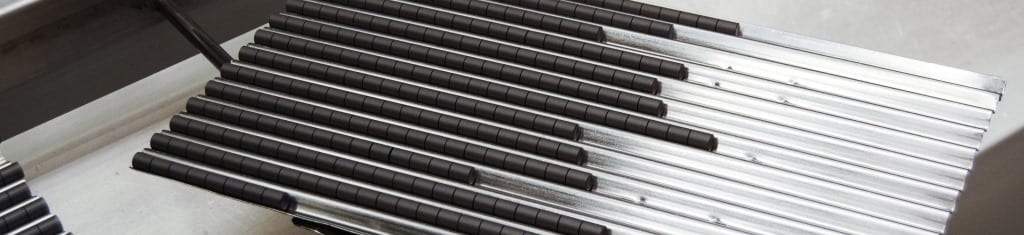
In another significant boost to commercial deployment of accident-tolerant fuel (ATF) at existing nuclear reactors, the first 18-month fuel cycle test of Framatome’s GAIA Enhanced Accident Tolerant Fuel (EATF) at Southern Co.’s Vogtle 2 has “demonstrated expected results and excellent performance,” Framatome said on Feb. 2.
Southern Nuclear installed four GAIA lead fuel assemblies (LFAs) containing EATF, both pellets and cladding, at Vogtle 2 in the spring of 2019, and plant experts removed the LFAs during a refueling outage in August 2020. Inspections have confirmed the EATF technology “performs to the industry’s highest standards,” Lionel Gaiffe, senior executive vice president with Framatome’s Fuel Business Unit, said on Tuesday. The trial is the first of three planned 18-month cycles of operation for the LFAs. “More detailed inspections and measurements are planned following the remaining two fuel cycles,” Framatome said.
The finding is a major milestone for the French nuclear technology giant, which is working to commercialize a near-term ATF design that involves chromium-coated zirconium alloy cladding with chromia (Cr2O3)–doped uranium oxide (UO2) fuel. The company is in tandem also developing silicon carbide cladding concepts. Framatome, which developed its GAIA EATF concept as part of its PROtect program and is part of the U.S. Department of Energy’s (DOE’s) EATF program, is targeting an aggressive timeframe to deploy EATF in the U.S. by 2022.
Framatome fabricated the GAIA fuel assemblies installed at Vogtle 2 at its fuel manufacturing facility in Richland, Washington, as part of a 2017 contract with Southern Nuclear. The assemblies, developed after numerous improvements, feature Framatome’s advanced chromium coating, which is added to its proprietary M5 zirconium alloy cladding. The combination “improves high-temperature oxidation resistance and reduces hydrogen generation in the unlikely event of loss of cooling,” the company explained.
The chromium coating also “offers increased resistance to debris fretting, reducing the likelihood of a fuel failure during normal operations.” Compared to previous fuel designs, the chromia-enhanced fuel pellets “have a higher density, reduced fission gas release and improved behavior under transient conditions. Reduced pellet-to-clad interaction also better supports power maneuvering, increasing performance for operators,” it said.
A Technical Triumph for Existing Nuclear
Framatome’s milestone, notably, is also a major win for the U.S. nuclear power industry, which is spearheading initiatives that improve cost and performance of the existing fleet to boost the competitiveness of nuclear power.
ATF is an industry concept used to describe new technologies in the form of new cladding and/or fuel pellet designs. According to industry group Nuclear Energy Institute (NEI), ATF fuels could increase efficiency, improve performance, and reduce operating costs because they essentially leverage new materials that improve fission product retention and are structurally more resistant to radiations, corrosion, and high temperatures. Because they could potentially extend the time between refueling from 1.5 to 2 years, ATFs promise to reduce the amount of fuel needed by about 30%, resulting in less waste and used nuclear fuel.
While ATF technologies have been under development since the early 2000s, they received a marked boost in the wake of the March 2011 Fukushima accident as the DOE aggressively implemented plans under its Congressionally mandated EATF program to develop ATFs for existing light water reactors. In a technology blueprint rolled out on Jan. 8, the Office of Nuclear Energy suggested it is working to deploy ATF in U.S. commercial reactors by 2025. The blueprint—which the Biden administration has yet to confirm it will back—envisions “widespread implementation” of ATFs by 2030.
So far, however, the DOE, an array of national labs, and power sector research entities have made remarkable progress working with Framatome, GE’s Global Nuclear Fuel (GNF), and Westinghouse to help commercialize their new fuels in the U.S. by 2025. The Nuclear Regulatory Commission (NRC), too, has confirmed it is preparing for anticipated licensing applications for commercial use of ATFs in U.S. commercial reactors.
Notable Accident Tolerant Fuel Progress
According to Pacific Northwest National Laboratory (PNNL), which is providing technical assistance to the NRC related to the newly proposed nuclear fuel and cladding designs, so far, GNF has tested several different iron-chromium-aluminum (FeCrAl) alloys (including Kanthal APMT, C26M, and MA956), as well as Abrasion Resistant More Oxidation Resistant (ARMOR) cladding.
In December, Oak Ridge National Laboratory (ORNL) received the first GNF-developed nuclear fuel test rods, which spent 24 months at Southern Co.’s Edwin Hatch nuclear plant. The test samples feature IronClad, an FeCrAl fuel cladding, and ARMOR, a hard, oxidation-resistant coating layered on top of zirconium cladding with UO2 fuel that GNF originally created outside of the DOE’s EATF program. “Initial visual inspections of the shipped samples showed no visible signs of flaws or degradation on either fuel concept after being removed from the commercial reactor,” the DOE said in December. ORNL is now slated to perform “additional testing on the test samples over the next year to gather the necessary data that’s needed to confirm performance requirements and to qualify the new fuel technologies with the [NRC],” it added.
Westinghouse is also working toward commercializing two near-term ATF designs under its EnCore brand. For near-term deployment, Westinghouse is testing chromium-coated zirconium cladding with chromium oxide-aluminum oxide (Cr2O3+Al2O3)—doped UO2 (ADOPT) fuel and chromium-coated zirconium cladding with uranium silicide (U3Si2) fuel. Westinghouse worked with Idaho National Laboratory to develop the silicide pellets. The company is, in tandem, working with General Atomics to develop silicon carbide (SiC) fiber–reinforced SiC matrix (SiC/SiC) composite cladding with high-density (U3Si2) fuel and other pellet designs including uranium nitride (UN).
Lead test assemblies containing Westinghouse’s concepts (12 rods with Cr-coated ZIRLO cladding and standard UO2 fuel; four rods with standard cladding and segmented U3Si2 fuel; and four rods with Cr-coated ZIRLO cladding and ADOPT fuel) were installed at Exelon’s Byron Unit 2 in Illinois in April 2019. According to PNNL, further lead test assemblies containing Cr-coated cladding with ADOPT, UO2, and U3Si2 fuels and SiC cladding with U3Si2 fuel are planned for irradiation in 2022.
Along with the 16 lead test rods with Cr-coated M5 cladding and Cr2O3-doped UO2 fuel that were inserted at Vogtle Unit 2 in spring 2019, Framatome’s concepts are also being tested at Arkansas Unit 1, PNNL said. In the fall of 2019, Arkansas 1 inserted 32 Framatome Cr-coated lead test rods. Meanwhile, two full assemblies with Cr-coated M5 cladding and Cr2O3-doped UO2 fuel are planned for insertion at Calvert Cliffs in spring 2021.
PNNL also noted that Framatome is “on track” for a 2025 “batch reload.” Plans are also underway to insert lead test rods with SiC/SiC cladding and Cr2O3-doped UO2 fuel are planned by 2022.
ATF R&D Advances Worldwide
ATF development around the world is also picking up steam. Under Japan’s ATF research and development (R&D) program, researchers are developing FeCrAl strengthened by the dispersion of fine oxide particles (FeCrAl-ODS) cladding, SiC/SiC composite cladding, and doped-UO2 fuel.
China has also developed several concepts, including both cladding (coated zirconium [Zr] alloy, FeCrAl alloys, coated molybdenum alloy, and SiC) and fuel (high thermal conductivity UO2). “Ex-reactor testing has determined some thermal and mechanical properties of these concepts,” PNNL said.
In South Korea, under the Korean Atomic Energy Research Institute (KAERI) and Korea Electric Power Corp. R&D programs, concepts under development include surface-modified Zr (Cr alloy-coated and oxide dispersion strengthened [ODS]), SiC cladding, iron-based alloy cladding, doped UO2 fuel, high thermal conductivity ceramic and metallic fuel, and TRISO-SiC composite fuel.
And in Russia, TVEL Fuel Co. in October 2019 completed the first phase of ATF testing at the State Research Institute of Atomic Reactors in the Ulyanovsk Region. The test involved two experimental ATF fuel assemblies with VVER (a Russian designed water-cooled, water-moderated reactor) and pressurized water reactor fuel rods.
—Sonal Patel is a POWER senior associate editor (@sonalcpatel, @POWERmagazine).
"fuel" - Google News
February 05, 2021 at 12:23AM
https://ift.tt/2MTDKKj
Big Boost for Framatome's Accident-Tolerant Nuclear Fuel - POWER magazine - POWER magazine
"fuel" - Google News
https://ift.tt/2WjmVcZ
Bagikan Berita Ini
0 Response to "Big Boost for Framatome's Accident-Tolerant Nuclear Fuel - POWER magazine - POWER magazine"
Post a Comment